News
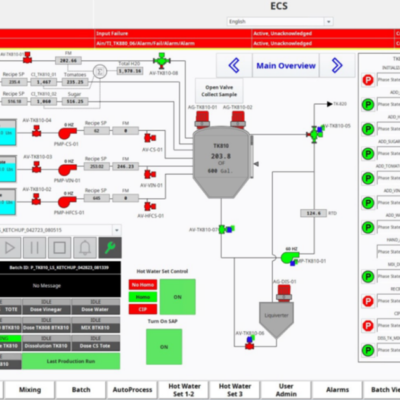
ECS & Ignition Deliver for AmeriQual
Success in many industries is the product of preparation and opportunity. Agility is frequently the lubricant that enables businesses to adapt and win a project or contract. This is especially true in private-label food manufacturing. “The people, processes, and equipment must be able to adapt to ever-changing market demands,” says Wes Blankenberger, Vice President of Operations & Maintenance for AmeriQual Group, LLC, in Evansville, IN (AmeriQual). Brand owners must beat their competition to market and the best way to do that is frequently via a capable private labeling partner. Much like brand owners leverage private label manufacturers, the manufacturing plants themselves leverage partners to assemble existing and new equipment into functional processing systems, often on aggressive timelines.
Similar traits and situations define success inside of the control system integration space. Much like private label manufacturing, clients call upon these firms because of their known ability to deliver in specialized market segments. They’re well-trained and typically gainfully employed by clients where they excel. Rarely are they entirely idle but their mix of professionals at different levels and specialties allows them to apply staff, often on short notice, to applications. Their highly trained teams can tackle projects or parts of projects large and small, often in concert with their teammates or outside firms.
Where these two examples overlap is the world where ECS Solutions, Inc. (ECS) thrives. For decades ECS has delivered solutions of all kinds to industry but none more frequently or more effectively than in batch processing applications. Batch projects never cease at ECS, and the DNA of the entire company reflects their dedication to this facet of manufacturing. Specialists in fields like pharmaceutical manufacturing have daily discussions about validation and operational qualification while water & wastewater-focused firms regularly converse about dissolved oxygen, head pressure, and lead/lag pumping systems. At ECS the daily conversations revolve around Equipment Modules, Recipe Procedure Models, and equipment availability. From entry-level technicians to the highest-order software specialists and project managers, ECS’ team is nearly guaranteed to work on multiple batch projects each year.
Much like a batch manufacturer’s capabilities are defined by preparation and availability, ECS prepares formally and maintains a high level of readiness through the regular use of its tools. One tool that their entire team knows well is Inductive Automation’s SCADA solutions. The scalable products from Inductive Automation are flexible enough to handle just about any industrial application so they are a frequent choice for the ECS team. Inductive Automation contributes to ECS’ readiness by providing a wide variety of training solutions for their Ignition products. “Every ECS teammate learns Ignition from the start of their tenure with us”, says Mark Randall, ECS Project Manager. “The fact that the training is online, free of charge, and modular allows us to use it upon hire at ECS and then regularly as a teammate matures in their capabilities,” Randall continues. Concepts and foundations are part of early phase Core training where highly specialized modules are executed later. Many at ECS achieve Gold certification which indicates that they have a deep understanding of and application knowledge of the tools.
Recently these worlds came together in a successful application for AmeriQual Group. Based in Evansville, IN, AmeriQual has an outstanding reputation for both innovation and quality so they are called upon by major food companies and the U.S. Military to provide packaged solutions. AmeriQual frequently states that “Quality is not just another goal; it is our basic strategy for survival and future growth”.
AmeriQual’s reputation for quality gets them opportunities to work on challenging applications. As such, they regularly partner with providers who have strong reputations for delivery and project success.
When presented with a chance to land a series of large contracts with a well-known label they quickly pressed all their assets into action to create an entirely new kitchen. They ordered long lead time items with less-than-optimal information available. Equipment that could be reused from their local storage cache was inspected, tuned up, and prepared for deployment.
Their existing relationships with local contractors allowed them to prepare the plant infrastructure immediately and quickly move into detailed piping and wiring. Perhaps most importantly, their relationship with ECS allowed them to quickly assess the project and create a framework so they could establish budgets and obtain bids. Of their initial meetings with ECS, Blankenberger states “We did a tour of the facility so they could see the operation firsthand and explained where we would like to get. From that ECS came back to us with ideas as well as showed us what their systems looked like and could do. We came up with a strategic path that could be implemented in a phased approach. The phased approach has allowed us to implement improvements to our operation in shorter timelines and simplify the training requirements for our team members”.
It was quickly evident that a fully integrated solution from ECS was not only possible but that it would be integral to long-term success. The solution would allow for as much effective automation as reasonable, thus minimizing the number of new operators to run the system once complete. “We didn’t consider using manpower temporarily because it is tough to find manpower and the processing requirements for the product would be challenging to accomplish by a person,” says Blankenberger.
With little more than a few preliminary conversations, ECS received an order in early January 2022. Working from preliminary P&IDs, the ECS team went to work using their methodical approach and vast experience in this arena to craft the solution. ECS knew they could deliver a flexible batch solution and they knew their best option would be Inductive’s Ignition platform. “This project encompassed a few elements that we’re uniquely positioned to address,” says ECS’ Randall. “The fact that it was batch processing put it squarely in our company wheelhouse and the fact that it was based on Ignition opened it up for many options within our team to be able to deliver the solution”, Randall continues.
ECS extended the capabilities of Ignition by developing custom faceplates within the system to tie into the control system running behind the scenes. “We have more than twenty custom faceplates in our Ignition library that we’ve deployed to tie into Rockwell’s PlantPAx process objects,” Randall states. “These allow us to apply standardized control functions to many similar items that are found throughout the control system. For example, code for instruments, VFDs, and similar equipment utilize pre-validated code and deploy efficiently”. The team has also developed an Ignition version of the Factory Talk Batch View Client, that uses Rockwell’s Factory Talk Batch API. This tight integration with Factory Talk Batch allows a high level of visibility into the batch operations without requiring additional software or switching client applications. “This level of integration allowed us to speed development in a way that keeps things from getting unruly. Our R&D and prior use of these elements really shone through on this project,” continues Randall.
In addition to the control and SCADA tie-in, ECS also had to address the multilingual requirements of the client. “We have approximately 20% of our staff that is Spanish speaking,” says AmeriQual’s Blankenberger. “ECS translated the system so that the operator interfaces could easily be toggled from English to Spanish depending on the team member. This has improved our team member’s willingness to work in this area of our facility as well as reduced training time”, he continues. The system not only presents the general-purpose automation in both English and Spanish, but the PlantPAx prompts are also mirrored as well. “We utilized the Localization capabilities within Ignition to accomplish the switching,” says ECS’ Randall. “Before we could do that, however, we used our native Spanish-speaking teammates to examine and tweak the generic translations that were delivered via software. Their adjustments add contextual value to the conversions that software alone cannot deliver. We know that batch operations require specific terminology and given effective direction, the pool of who can work these departments for our clients grows in depth and quality,” Randall concludes.
When asked about the relationship between ECS and AmeriQual, ECS’ Randall states “We could not have asked for a better partner in this than AmeriQual. The aggressive timeline situation was created by the end clients’ demand, but AmeriQual’s knowledge and professionalism set them up as a phenomenal partner on this,” he continues. AmeriQual’s Blankenberger agrees, stating “Transparency, accountability, and communication. These attributes are critical for projects with short timelines. AmeriQual and ECS were true partners in the project. There were many challenges and tough discussions throughout the project but we were able to make decisions and prioritize tasks based on what was best for (the project)”.
The project came together successfully on a very aggressive timeline. “I thought the batch system would be ready on time for testing to begin but would have quite a few bugs to work out due to the short timeline and complexity of the system,” says AmeriQual’s Blankenberger. Instead, the ECS solution was delivering high-quality, finished batches upon the first week of launch. When asked how the project was able to succeed, ECS’ Randall indicates that the depth, readiness, and adaptability of the ECS team put them in a unique position to deliver this. ECS’ rich history in batch manufacturing and deep knowledge of their Ignition toolbox certainly framed them as the best solution for this application. Thus, at the confluence of preparation and opportunity, is another successful project built on Ignition and delivered by ECS Solutions.
Download this Case Study Here!
Posted In: Case Studies, Chemical Industry, Uncategorized