News
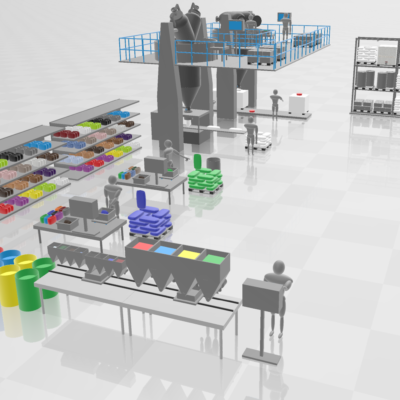
Materials and Lot ID Traceability
In the event of a recall can you find everything you need to know in an expeditious way.
As per Wikipedia, “Traceability” is the capability to trace something. In some cases, it is interpreted as the ability to verify the history, location, or application of an item by means of documented recorded identification.
In the process industry, we are required to know the whereabouts of the raw and intermediate materials as well as the finished products. This is paramount since recalls can be impactful to the safety of the consumer as well as financially to the producers.
The activities required to maintain the necessary information as well as creating reports can be performed manually by the production personnel or may be an integral part of the automated manufacturing process. Automating the process to perform tracking and tracing greatly reduces the risks since issues created by people inaccurate activities are eliminated, but many processes are highly manual, these can be greatly improved by applying a semi-automated tracking system.
A semi-automated system interacts with the operators by providing them clear instructions on the activities that need to be performed. The activities can incorporate the entire product manufacturing instructions that include material movements, these are clearly specified, from what source to what destination, amounts, these transactions can include capturing information such as Lot ID, vendor, material properties. All activities are electronically journaled including ingredients consumed during a production process, intermediate materials as well as finished products. These semi-automated systems can also interact with the ERP system to receive work orders, execute them and inform of material consumed, and show work orders produced.
Off-the-shelf products enable the integration of your plants’ Ecosystem including the ability to determine where every material is, whether in storage, in-process, or finished product. This can then be used to perform material reconciliation reports but most importantly to shorten time and cost of identifying and notification in the event of a product recalls. Can you expeditiously create records of compliance?
Posted In: Bakery Industry, Batch Boosters, Beverage Industry, Chemical Industry, Distilleries, Food Industry, Life Science Industry, White Papers