News
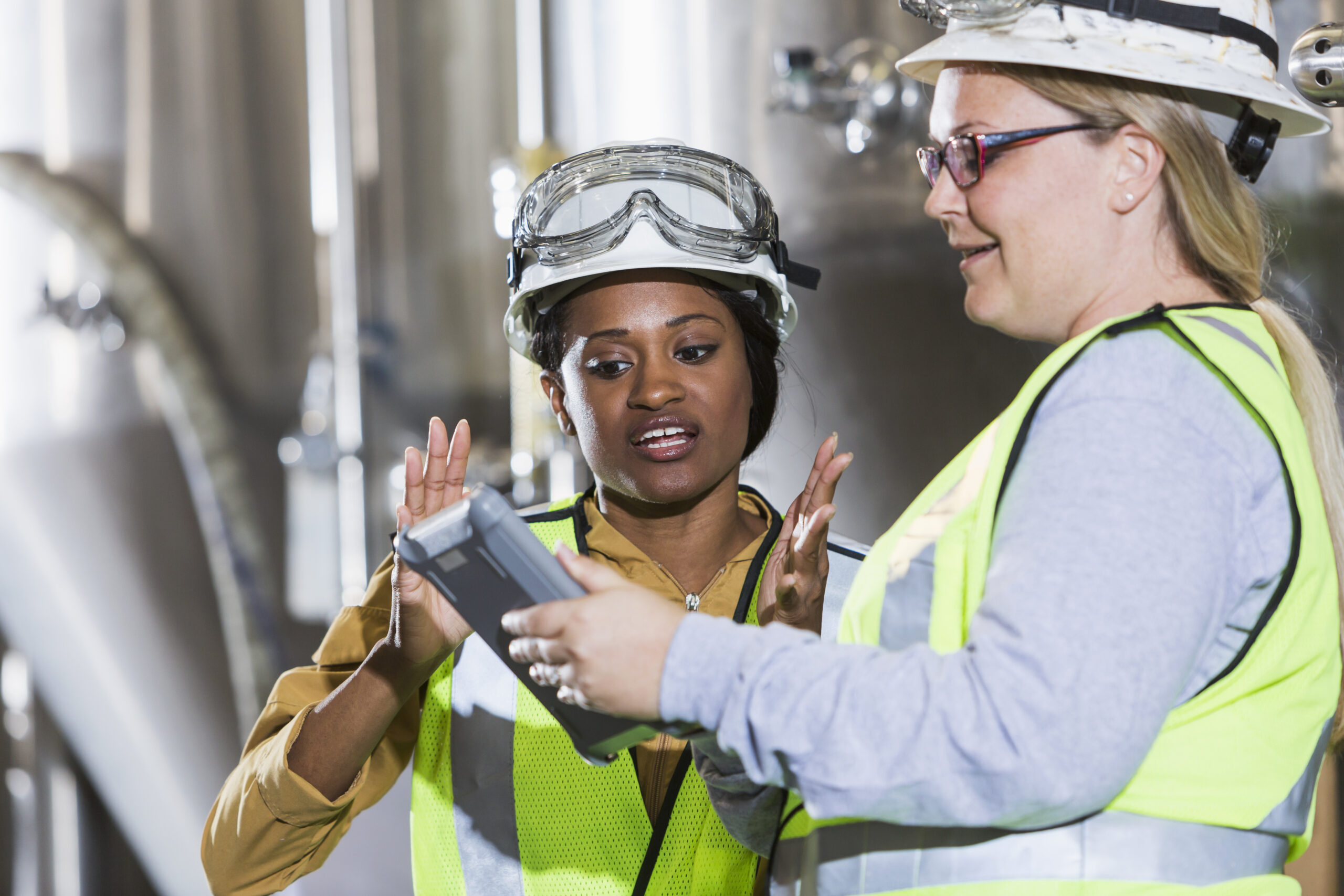
Embracing the Connections of Automation Projects
The ECS Solutions (ECS) team works on all manner of automation projects, from small to large and from very simple to highly complex. Many of these projects have a major impact on the success of their clients but few are more satisfying than when a project’s results are a dramatic streamlining of plant operations tied in seamlessly with new or upgraded automation.
The most effective manufacturing companies enjoy a harmonious tie-in between the automation that exists, regardless of the level or magnitude, and the other systems that complete the plant operations. Standardized procedures, reduced waste & increased quality, compliance with contracts and regulations, and better employee contribution are all hallmarks of the best manufacturers, and all lead to increased profits.
Most companies have some degree of automation, some at only a single machine or line level, while others are more hands-off. Fully automated, “lights out” operations exemplify this to the extreme, but this type of factory is much more the exception than the norm. The level of automation and connectivity to other plant departments is often dictated by the complexity of adjacent operations and how these systems interact.
Major automation projects can be a perfect time to review not only how products are made but also how the manufacturing systems are connected to the rest of the plant. These projects are typically among the larger endeavors, both financially and operationally, that an organization will undertake. They necessitate a level of study and review of the entire manufacturing process including all transactions and documentation. ECS is well-versed in both physical automation as well as the interface between other plant systems and that expertise can be an enormous benefit to clients. They have worked for decades on successful projects that enhance both physical automation and other operations. Moreover, they have learned to embrace the concept that there is an enormous amount of valuable information regarding the most efficient way to operate all tied in the minds of the teams that run different aspects of a plant. Departments like Production, Quality, Maintenance, and Inventory all should be considered. This approach helps to ensure the success of the physical automation endeavor by generating excitement for the core project, enforcing camaraderie between departments within the plant, and raising the success rate of the entire effort by creating a collaborative environment.
Recently ECS was brought into a canning operation by a longtime OEM partner. The initial request was a line SCADA application and that was the primary deliverable. The client wanted more once ECS met with them and described the possibilities for finished operations as well as the process that they use to accomplish the overall integration work. They decided to use the incoming automation as a catalyst to push all their activities forward. Working with ECS they mapped every critical function and examined precisely how it would tie into the new line and they leveraged the opportunity to streamline everything. Every transaction and administrative step was examined, and a proactive approach was taken to digitize those activities. Elimination of duplicate actions as well as all unnecessary paperwork were overarching goals.
The ECS team also leveraged their broad experience to utilize everything they could that already existed within the facility. The plant’s ERP connections, existing RFID employee badges, and other tie-ins were considered at the suggestion of the departmental leads. These connections all became part of the end solution. Jointly they investigated better options for project elements and the client was empowered by the result. For example, at ECS’ guidance, the client’s team explored the potential of multi-screen, highly capable manufacturing televisions versus the originally planned simple displays. The client opted for a better solution that they chose and that they had input over the contents of. True ownership of that element resides wholly with the plant personnel and the department leads who drove that selection and design.
ECS’ project manager developed critical documentation from the workshops and client meetings and these documents became the project’s “bible.” Revisions happened in a structured manner and the final product was agreed upon by all, thus, no surprises. These steered the entire project team from development through to final implementation.
There are few types of projects that generate as good a feeling for an ECS project manager as one like this. People and departments who may not have expected benefit of an automation effort later revel in what the collective team achieves. The client’s fingerprints are all over the project and the benefits spread throughout the operation. The end client’s overall goals are exceeded because of the collaborative strategies led by the ECS team and implemented by all involved.
Posted In: Case Studies, Food Industry, SCADA