News
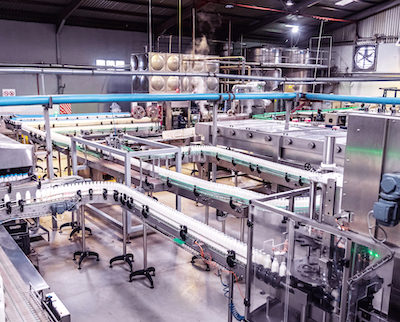
Systems Integrator Extends Packaging OEM’s Reach
Modern packaging plants want tightly integrated line solutions that run their array of products with fewer operating personnel and the easiest possible means for equipment maintenance. Buyers increasingly purchase large-scale packaging solutions from a single vendor with the expertise to deliver these applications. This presents challenges to equipment OEMs, many of whom offer a few niche or high-level equipment with a menagerie of complimentary machines. Many project suppliers are chosen based on their proven ability to handle a specific, complex operation around which the line is anchored, and the additional machines become part of the overall project by default.
It is generally not feasible for focused machine OEMs to also provide the broad-reach solutions required to fully integrate these complex lines. The breadth of staff required to achieve the expertise for detailed machine control along with the adjacent line operations and IT connections would be unbearably expensive for most machine builders. This is especially true because fully integrated options are not part of every option, so OEMs end up with some of their highest-end staff idle on many of the simpler applications that they tackle. These extended solutions frequently come via a dedicated line systems integrator. ECS Solutions (ECS) is a systems integrator that has delivered a huge variety of manufacturing solutions for more than 45 years including highly integrated packaging lines.
OEMs have specific abilities to design, modify, and support their equipment. They bring a high level of packaging equipment and operations to applications, leveraging their intimate knowledge of packaging and line specifics. They are frequently the best solutions for the purchase of individual machines and small cells as well as the support of that equipment. As the lines or solutions become more complex, a systems integrator can help in expanding the OEM’s reach. One way they can provide their turnkey solutions in all manner of situations is via a partnership with a seasoned integrator like ECS. The ECS team augments its core staff when they need to offer extended solutions.
A properly designed ECS line integration system allows the user to enjoy all the flexibility offered by all the line’s equipment. The ECS solution ensures that the machinery transitions from product to product, order to order with minimal input and required adjustments. Optimized performance, ease of changeover, streamlined maintenance functions, and more can come from a proper integrated system.
In a recent canning line control application, delivered in partnership with a worldwide packaging OEM, ECS delivered an Ignition solution that united all the line’s equipment into a cohesive system. All the line’s machines communicate to the Ignition line control application via standard drivers and schemes. This connectivity, along with the line control code, provides the best possible control solution and machine-to-machine information exchange. Line starts, planned and unplanned shutdowns, and restarts all happen with maximum efficiency and the best possible information about normal and abnormal operations. Strategically placed operator interface terminals (OITs) steer the streamlined operating staff to items that require attention at locations where they can have the maximum impact for input and problem resolution.
Perhaps the most powerful benefit to ECS’ involvement in this project was their deep background in industrial IT. In addition to the physical line control, ECS developed all the middleware to facilitate communications to and from the end client’s Adage ERP system. Work orders flow easily from the ERP to the Ignition line control and finished information returns during and after a product run. This allows lot tracking to the pallet level or better. The level of integration also provides a huge reduction in the amount of paperwork involved with the process. Standard, quality, and discrepancy interfaces which are paperwork intensive elsewhere in the plant are all electronic on the new line. This provides both easier operation and more accurate storage of manufacturing data.
Since the line control addresses the entire line rather than machine by machine, the line deployed with full data collection and OEE which help the client benchmark operations from the first day of production. This is proved enormously helpful for the development of operating staff as this project represents a huge technological leap forward compared to the other dozen lines in the facility.
ECS’ IT prowess is evident elsewhere in the project with secure, full-line network, the implementation of EWON full-line remote access device, integrated RFID login tools that utilize existing, in-plant badge technology, and detailed overhead television solutions which guide warehouse personnel. The overhead TVs show real-time performance data from the Ignition application which help all staff understand how the line is performing with a simple glance. These units also display relevant warehouse information directly from the Adage ERP for required consumables such as labels and finished goods storage data.
The result of this application is a flexible solution that matches the required flexibility of the canning line itself. The end client enjoys a level of interface and simple operation that is nearly inverse of the complex line to which the systems interface. The team of the OEM and ECS has proven to be the best element of the entire packaging solution.
Posted In: Case Studies, Food Industry, Inductive Automation