News
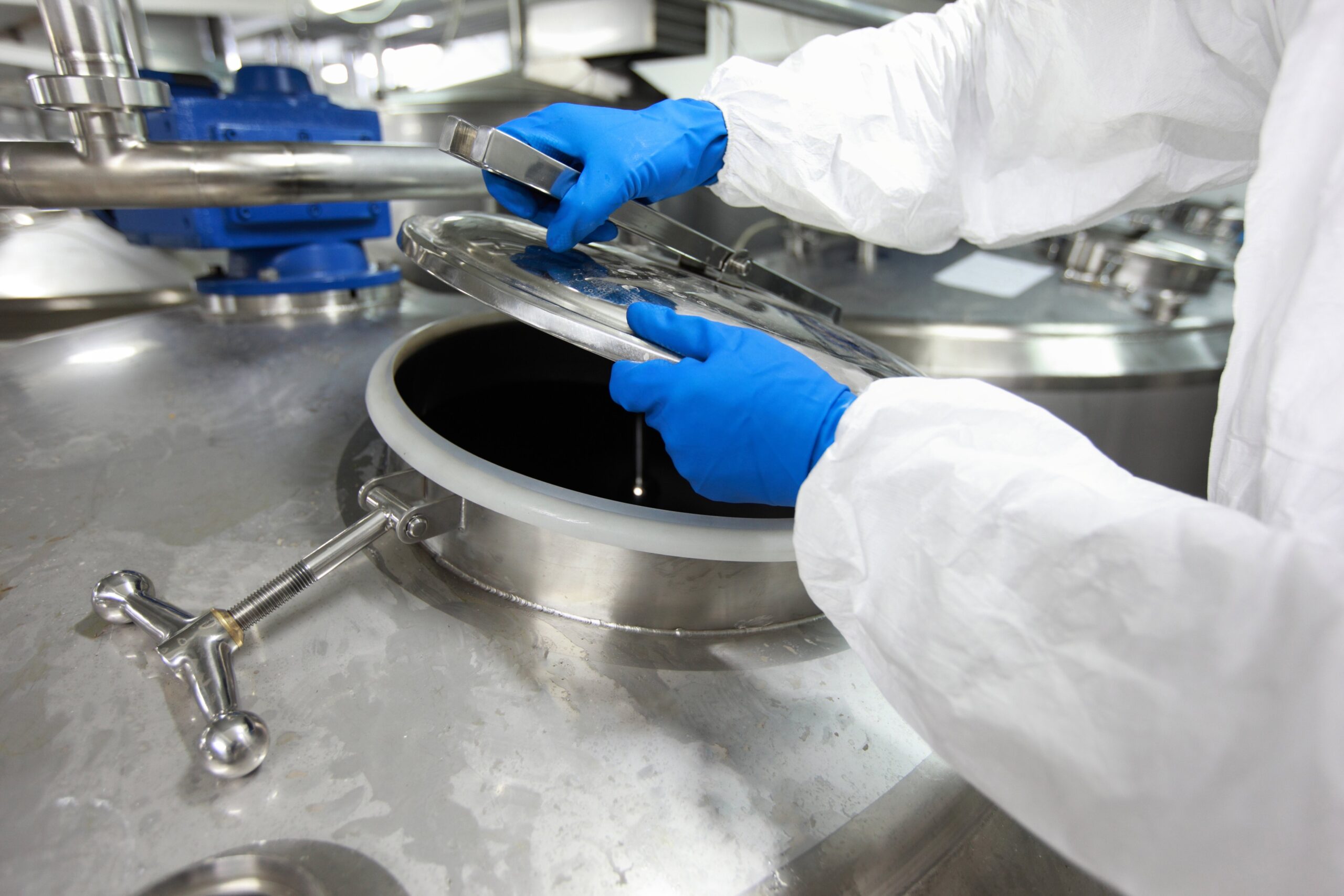
Manual Ingredient Additions – Confirmation and Tracking
ECS Solutions, Inc. (ECS), worked with a world leader in nutritional products to tie together the most critical software tools used in their dry ingredient manufacturing. This project merged the capabilities of the existing inventory tracking system with the robust batch processing capabilities in the company’s final assembly area.
The client’s existing inventory management system is a reliable platform which facilitates comprehensive materials tracking, complete with connectivity to their SAP ERP. The final assembly area FactoryTalk View batching system is a prompt-driven batching application designed to steer operators towards the successful assembly of mixes. The overarching goal of this project was to further enhance the consistency in product mixing actions by every operator. ECS tied, the tried and tested inventory tracking functions of the inventory management application, to the programmatic and physical control points provided by the batching control system. The results are streamlined operations for mixing personnel, non-invasive enforcement of the mixing steps and procedures, and more complete data records regarding specific ingredient usage and batch performance.
Historically, each of the existing systems utilized their own user interface terminals and operated relatively independently from each other. The client desired additional connectivity that allowed new and critical functions to be merged between the disparate systems. Operators are now prompted to identify via barcode scan specific ingredients which will be used in a given mix. This is the ingredient verification portion of the revised system. This ensures that the proper ingredients are not only known and planned, but that they are physically on hand and ready to be introduced, when directed, to a current mix. This includes identifying both the bulk ingredients and any required pre-weighed materials. Later, during the ingredient addition portion of the revised system, the added control system functionality demands that operators re-scan the ingredients before they can be dispensed or manually deposited into the mix. To take the functionality beyond the manual operations which were used in the past, the improved system integrates with the controller’s logic so that new interlocks programmatically prevent the dispensing of bulk ingredients. Similarly, manual additions of pre-weighed minor ingredients are more tightly enforced by engaging interlocks until scanning requirements have been met.
This new functionality, which includes an active connection to the inventory system, has been added to the batching control system’s user interface (HMI). This supported a primary goal of the project which was to simplify operations between the two systems for operators. As a result of this work, operators now utilize the batch system HMI only for all required functions. This streamlines production operations and provides a single point of maintenance for the management of operator training as well as potential future functions. The legacy inventory management terminal is now used only when advanced functions, typically beyond the daily requirements for operators, are necessary.
The physical automation tie-ins were accomplished via an Ignition software bridge to the automation system. This powerful connection provided a platform for the integration of new, area-dedicated barcode scanners which enable critical mobile operations while providing go/no-go feedback via on-board LED indicators and audible beep patterns. The automation connection also provides the basis for interlock control via solenoid powered lid locking mechanisms which is used to allow introduction of the bulk and pre-weighed minor ingredients only if all conditions are met. Further, this interlocking facilitates strict batching controls which may require specific timing related to the introduction of ingredients or required timing for related functions like latency or operational timers. All user interactions are time stamped, a move which eliminates the potential of material usage information being recorded only after a batch is already complete. Supervisory override functions were also added to assist in the event of anomalies, allowing the barcode scanning enforcement to be bypassed in favor of traditional tracking methods if necessary.
This pilot project focused on the final point of use of materials by operators, as described previously. Elsewhere in the facility, mixing personnel create craft bags of intermediate ingredients that are later used in finished product mixing operation. This process, as an example, utilizes a much simpler control system that does not require the fullness of features implemented for the final assembly process described above. In this reduced architecture, the control system maintains connectivity to the overarching inventory management for what equates to “permission to proceed,” while continuing to allow the related terminals to be used for all material scanning and tipping activities. In this way, the control system is modified to wait for confirmation of material usage but does not seek to replace or replicate the functionality of the inventory terminals entirely. An upcoming phase of the project will implement a simpler but similar set of controls to these areas. This modification to the solution has already been developed and tested and will be deployed in upstream processing areas within the same facility.
Software related to manual operations in a factory environment is only valuable if it enhances the experience for the operators or if it adds to quality to the finished products. These legacy products have done both for this ECS client for a long time. Now, with the addition of the integration from ECS Solutions, both of those criteria have been satisfied yet again and to a higher level. The organization now stands poised to propagate this new level of integration and productivity throughout additional manufacturing processes and sites.
Posted In: Bakery Industry, Beverage Industry, Case Studies, Chemical Industry, Consumer Goods, Distilleries, Food Industry, Inductive Automation, Life Science Industry, Metals, Metals Industry